Mink Fur Production Process and Craftsmanship
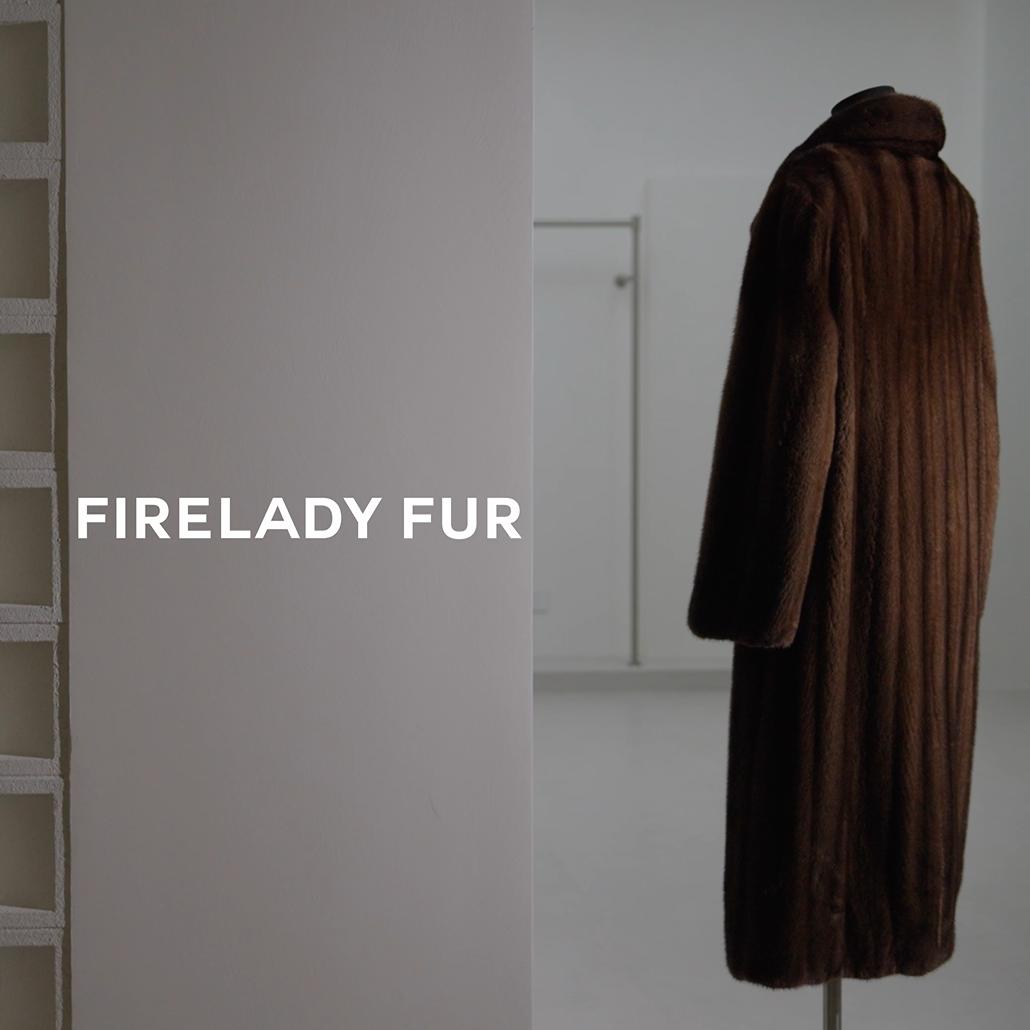
1. Skinning:
Remove the head, tail, and limbs, retaining the best parts from the middle.
2. Inspection:
Remove any uneven parts after sewing and re-examine for re-skinning and sewing.
3. Retanning:
Also known as applying the leather solution, this step makes the leather board resistant to high temperatures, preventing deformation and avoiding decay or damage after prolonged wear.(Clothes not treated with retanning may develop odors and leather decay after half a year or a year.)
4. Inspection:Check for smoothness, puncture marks, and other issues.
5. Stretching Process:
Stretch the fur to ensure that the finished garment is flat and does not curl.(Not stretching the mink fur to reduce costs is avoided.)
6. Drying:
Following traditional methods, sun drying is optimal, or drying in a steam room with a temperature of around 60 degrees and humidity around 60%.(Even temperature and humidity ensure the fur and leather sides are soft with some moisture, and appropriate grease content is preserved.)
7. Water Penetration Process:
Enhances the luster of the fur, ensures uniform direction of hair needles, and prevents hair from exploding.
8. Color Matching Process:
Due to a large amount of purple label mink, the colors are pre-dyed half a year in advance. For example, to make 50 pieces of clothing, select from 200 pieces of mink fur for color, luster, texture, thickness, and leather board thickness and softness.We will categorize based on the overall intention of 200 pieces into 5 to 8 subtle categories. Under such detailed classification, each mink's color, thickness, and luster are very similar.
9. Leather Matching Process:
In a breakdown of 5-8 categories, based on different styles and mink usage, select 15 to 20 of the closest mink skins for each category to make clothes.
10. Inspection:Check for smoothness, puncture marks, and other issues.
11. First Nailing Sample Process:
The garment has been made according to various parts, and the first warm setting sample ensures each part is further shaped.Drying Inspection: Check for smoothness, puncture marks, and other issues.
12. Second Nailing Sample Process:
After washing and water completion, ensure the sample is consistent and needs a second nailing to ensure complete shaping without changes.Then drying.
13. Water Penetration:
Enhances the luster of the fur, ensures uniform direction of hair needles, and prevents hair from exploding.
14. Full Sample:
(Sample on - shell) Remove excess edges and corners of the garment template, and create a model for the edges and corners.
15. Fur Rolling Process:
(Imported professional equipment washes the mink leather board and mink fur, making the fur shiny and the leather board soft and delicate.)
16. Ironing:
Before attaching the lining, iron the entire garment to make it more flat.
17. Lining (Silk Lining):Make the silk lining.
18. Hand Sewing Process:
All parts and linings are sewn together by hand to complete the garment.
19. Final Inspection:
Check if the finished garment meets quality requirements and if all parts' data conforms to the garment's data requirements.
20. Removing Fluff:
Remove a small amount of knife-cut hair caused by the expansion of hair follicles during the production process.
This detailed process ensures that each mink fur garment is crafted with precision and care, resulting in a luxurious and high-quality product.